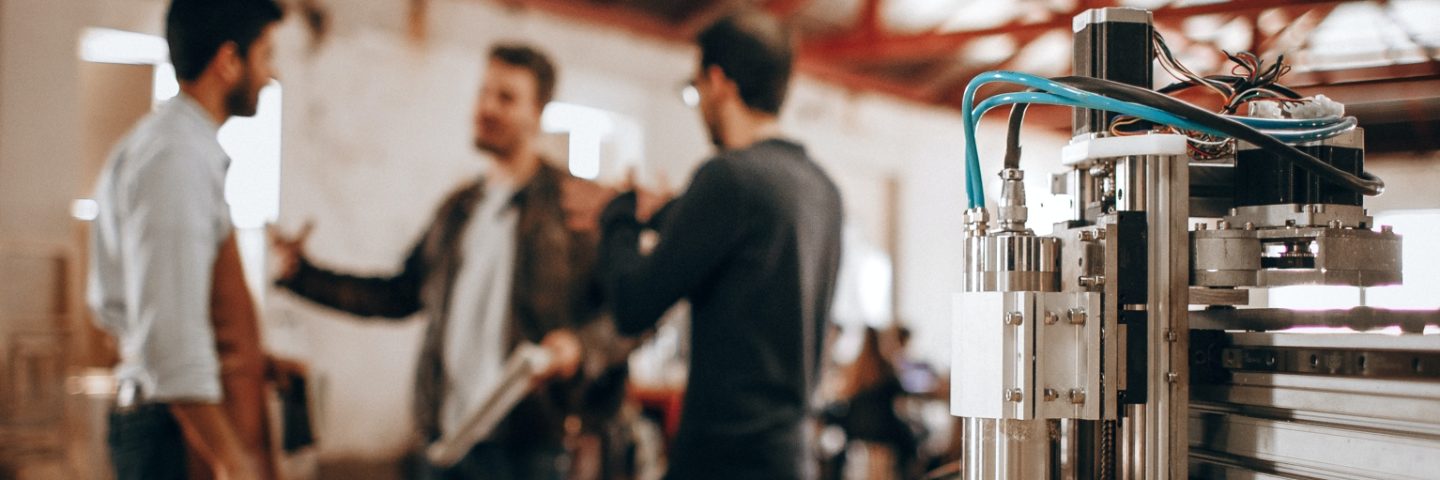
Value stream mapping voor productiebedrijven: zo breng je je bottlenecks in beeld
Bij elk productbedrijf staan optimalisatie en efficiëntie centraal. Tijd is geld en het minimaliseren van verspillingen en kosten is essentieel om als productiebedrijf winstgevend en relevant te blijven. Dit is waar Value Stream Mapping (VSM) om de hoek komt kijken: een procesanalysetool die processen visualiseert en zo verborgen verspillingen identificeert. Maar VSM is geen wondermiddel. In dit artikel verkennen we VSM als praktische tool met alle voordelen en gebreken.
VSM: waar hebben we het precies over?
Value Stream Mapping is een visuele weergave van de processen die betrokken zijn bij de productie van een product, van de initiële conceptie tot de levering aan de klant. Het geeft de volledige waardestroom van een productieproces weer en legt de focus op het elimineren van verspillingen en verbeteren van efficiëntie. Met VSM kan een productiebedrijf snel zien waar verbetering nodig is en wat er moet veranderen om deze te bereiken. Vooral de onderlinge afhankelijkheid tussen deelprocessen bieden waardevolle inzichten.
Neem bijvoorbeeld een productiebedrijf dat telefoons produceert. Om te zien waar verspillingen en inefficiëntie zich voordoen, analyseer je met VSM de gehele waardeketen. Vanaf de aankoop van de grondstoffen tot aan de verkoop aan de klant. Zo zal Apple na alle problemen met Foxconn, werelds grootste fabrikant van computeronderdelen, anders kijken naar de impact van werkomstandigheden op de productie.
VSM is voornamelijk geschikt voor productiebedrijven, waar de waardestroom van het product duidelijk is en de processen relatief gestructureerd zijn. Bedrijven die zich bezighouden met de ontwikkeling van nieuwe producten of diensten kunnen minder baat hebben bij VSM.
VSM als onderdeel van Lean en Six Sigma
VSM wordt gezien als een van de belangrijkste hulpmiddelen van de Lean filosofie, die gericht is op het creëren van waarde voor de klant door het minimaliseren van verspillingen en het verbeteren van de efficiëntie van processen. VSM werd oorspronkelijk ontwikkeld in Japan in de jaren ’50 door Taiichi Ohno van Toyota, maar het werd pas populair in de jaren ’90 toen John Shook van het Lean Enterprise Institute het concept introduceerde in de Verenigde Staten. Het idee achter VSM is gebaseerd op de Theory of Constraints, een managementfilosofie die stelt dat het verbeteren van het zwakste onderdeel van een systeem de efficiëntie van het hele systeem verbetert. Deze kritieke factoren worden beperkingen of bottlenecks genoemd. VSM wordt vaak gebruikt in combinatie met andere Lean-tools en -technieken zoals Kaizen, 5S en Kanban.
VSM kan ook worden gebruikt binnen de Six Sigma methodologie, die gericht is op het verbeteren van de kwaliteit van processen door variatie te verminderen. Het helpt organisaties om processen te verbeteren door middel van data-analyse, statistische technieken en continue verbetering. Het gebruik van VSM in Six Sigma stelt organisaties in staat om hun processen beter te begrijpen en te optimaliseren om defecten te verminderen en de kwaliteit van het eindproduct te verbeteren.
Wanneer is VSM wel en niet interessant voor productiebedrijven?
VSM biedt een visualisatie van de huidige processen waardoor verspillingen en inefficiëntie snel geïdentificeerd kunnen worden. Dat leidt tot een beter begrip van de productiestroom waardoor de samenwerking tussen teams verbetert. Typisch leidt het implementeren van VSM tot een efficiëntere productie, minder verspilling, kortere doorlooptijden en hogere kwaliteit van het product.
Natuurlijk zijn er ook nadelen verbonden aan het gebruik van VSM. Het kost bijvoorbeeld veel tijd en moeite om een volledige VSM-analyse te maken en het kan lastig zijn om alle benodigde informatie te verzamelen. Wanneer je te veel tijd besteedt aan het visualiseren van het proces, gaat dat ten koste de tijd die nodig is om het proces daadwerkelijk te verbeteren. Aan de andere kant kunnen onvolledige gegevens leiden tot verkeerde conclusies en verkeerde beslissingen. VSM vraagt dus om het balanceren tussen het verzamelen van genoeg informatie om de juiste conclusies te trekken, en niet teveel informatie verzamelen waardoor je kostbare tijd verspilt.
Bovendien kan het visualiseren van processen resulteren in een te simplistisch beeld van de werkelijkheid. Productie blijft mensenwerk.
Hoe zet je VSM efficiënt in? 5 Best practices
Vanuit de dagelijkse praktijk van Blom Consultancy komen de volgende best practices die je tijd en moeite zullen besparen bij de inzet van VSM en die zorgen voor betere resultaten:
- Waar wil je heen? Begin met het definiëren van de scope van het proces dat in kaart wordt gebracht. Bepaal wat de belangrijkste doelstellingen zijn die je wilt bereiken met VSM en bepaal welke activiteiten wel en niet binnen die scope vallen.
- Werk met een multidisciplinair team: Het team moet bestaan uit mensen die betrokken zijn bij het proces, vanaf het begin tot het einde en die de verschillende deelprocessen in het productieproces begrijpen. Dit betekent dat er medewerkers van verschillende afdelingen betrokken moeten zijn, zoals inkoop, productie, kwaliteitscontrole en logistiek. Idealiter betrek je het hele productieteam bij het VSM-proces, zodat iedereen beter inzicht krijgt in het productieproces en gezamenlijk kan werken aan verbeteringen.
- Identificeer de verspillingen: verspillingen zijn activiteiten die geen waarde toevoegen aan het productieproces. Veelvoorkomende voorbeelden van verspilling zijn overproductie, wachten op onderdelen en overbodige verplaatsing.
- Focus op de doorlooptijd: dit is de tijd die nodig is om een product van begin tot eind te produceren. Het is essentieel om de doorlooptijd te begrijpen en te identificeren waar vertragingen optreden. Door vertragingen te identificeren, kun je de knelpunten in het proces oplossen en de doorlooptijd verkorten.
- Visualisatie is een hulpmiddel: een stroomdiagram is een visueel hulpmiddel dat het productieproces in kaart brengt. Het helpt om het proces inzichtelijk te maken en die gebieden te identificeren waar verbeteringen kunnen worden aangebracht. Let er wel op dat het slechts een hulpmiddel is, en geen doel op zich.
- Blijf continu verbeteren: VSM is een doorlopend proces. Blijf het proces herhalen en bekijk regelmatig of er nieuwe verbeteringen mogelijk zijn. VSM is bovenal een hulpmiddel om continu te verbeteren en het is niet de oplossing voor alle problemen.
VSM gaat over nu en straks
VSM gaat niet alleen om de huidige toestand, maar ook om de toekomstige staat. VSM is alleen effectief als het wordt gebruikt als een continu verbeteringsproces, niet als een eenmalig project. Pas je VSM op terugkerende basis toe, dan kun je ook de verbeteringen die je hebt doorgevoerd toetsen en weer aanpassen waar nodig.
Reacties